Non-destructive testing (NDT)
NDT is fundamental in ensuring the safety of assets for personnel, environment and investors.
Failure of a component, structure or weld can cause significant hazard to the environment and often leads to significant costs.
Ensure safe, continuous and cost effective performance of your asset, basing your decisions on reliable NDT-data on the assets condition.
We deliver NDT services to all industries during fabrication, in-service as well as during shut downs and maintenance
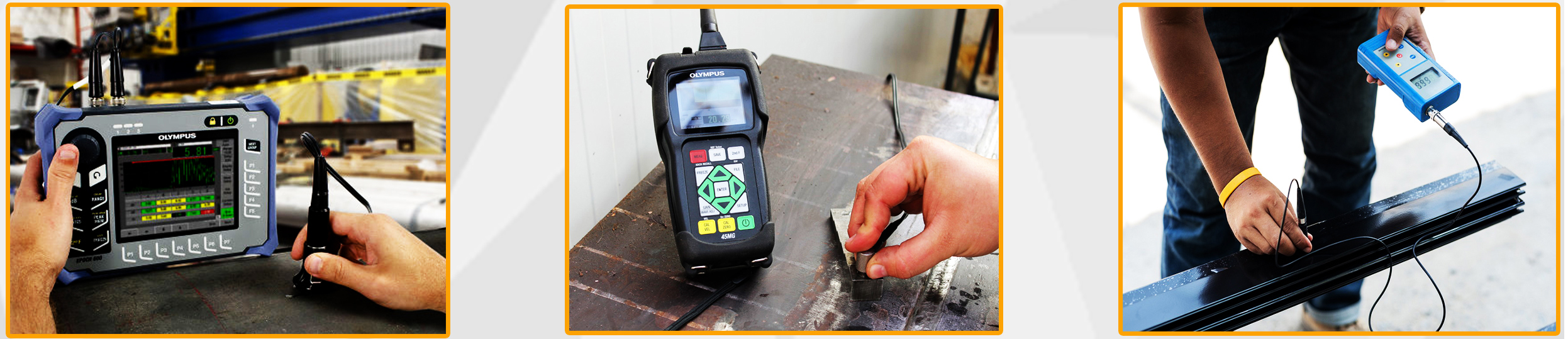
Conventional NDT
- Visual Inspection-VT
- Dye/ Liquid penetrant inspection-PT
- Magnetic particle inspection-MT
- Radiographic inspection-RT
- Manual ultrasonic inspection
- Ultrasonic flaw detector
- Ultrasonic thickness measurement
- Painting & Coating inspection
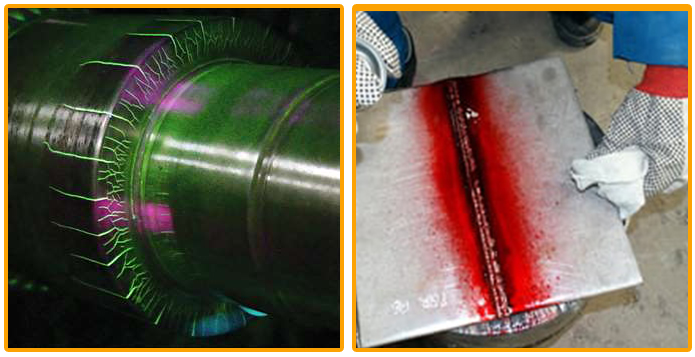
Ultrasonic flaw detector
One of the most common techniques to identify defects is ultrasonic inspection where sound waves, propagated through the material, are used to identify such anomalies.
The high frequency sound behaves predictably when interacting with surfaces and internal defects.
Flaw detection can be applied in almost any industry from composites and metals , to petrochemical oil and gas pipelines and storage tanks, to power generation. The most common anomalies detected include cracks, voids and porosity in metals, ceramics and plastics in addition to delamination and disbands in composites.
Advantages of ultrasonic testing include:
• Access is only required from one side for pulse-echo mode
• The depth of penetration is superior to other methods
• Highly accurate flaw sizing and shape
• Minimal part preparation is required
• Results are in real-time
Advanced NDT
Coyaps has an extensive range of Advanced Non-Destructive Testing equipment that offers our clients an unmatched capability of applications ranging from weld inspections to the detection of hidden cracks, voids, porosity and other internal irregularities in metals and composites.
Our specialized applications will help you to enhance inspection quality, simplify processes, speed up your inspection setups and realize easier interpretation.
With our state-of-the-art inspection technologies & application methods, you will save overall maintenance costs, improve production quality and ensure reliable operating processes.
Advanced NDT Techniques
1. Phased Array Ultrasonic Testing (PAUT)
2. Time of Flight Diffraction Testing (ToFD)
3. Corrosion mapping using Phased Array UT (C Scan, B Scan)
4. Eddy Current Testing (ECT)
5. Remote Field Electromagnetic Testing (RFET)
6. Internal Rotating Inspection System (IRIS)
7. Near Filed Testing (NFT)
8. Tank floor bottom plate scanning by using Magnetic Flux Leakage technique (MFL)
9. Long Range Ultrasonic Testing (LRUT)
10. Wire Rope testing 11. Remote Visual Inspection (RVI)
12. Pulsed Eddy Current (PEC)
13. Corrosion Under Insulation (CUI)
14. ECT weld surface inspection
15. Ultrasonic thickness measurement at High temperature
Supportive services
• Vacuum Box Testing
• Hardness Testing
• Post Weld Heat Treatment
• Rope Access Services
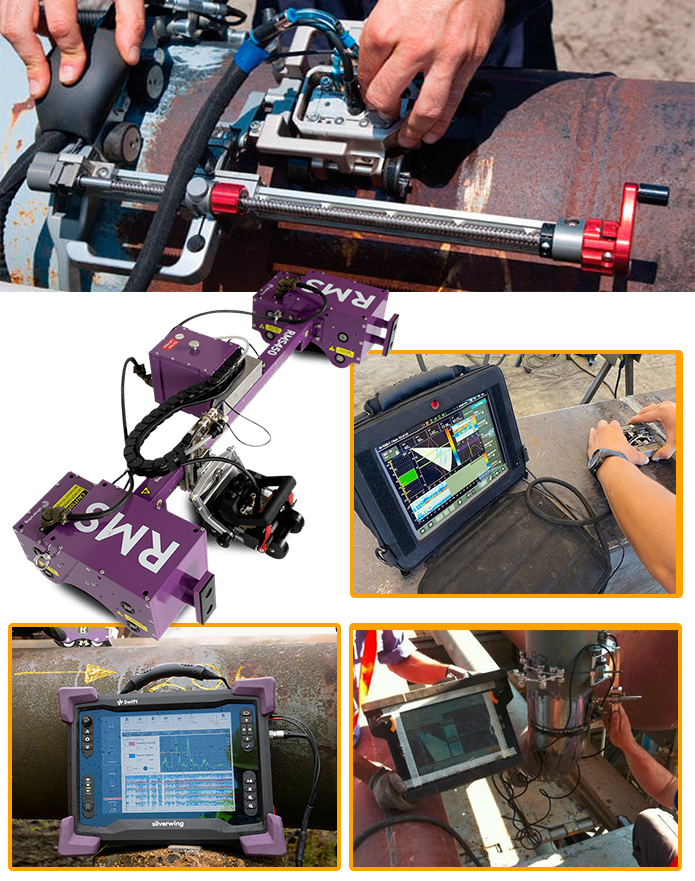
Non-destructive testing (NDT) covers a broad group of techniques used to evaluate the properties of a material, part, product, weld, or system without materially affecting the integrity of the unit being inspected or investigated under the test procedure. The non-destructive testing methods we offer are designed to comply with a variety of industry standards, unique customer requirements, government contracts.